Rice Processing Moisture Measurement
Measuring moisture during the processing of rice is recommended in several places, including raw material intake, conditioning, drying, finishing, and packaging. Moisture control contributes directly to delivering a consistent final product and allows energy optimisation.
Typical Applications
Typical Materials
- Rice
- Paddy rice
Related Products
Key Benefits
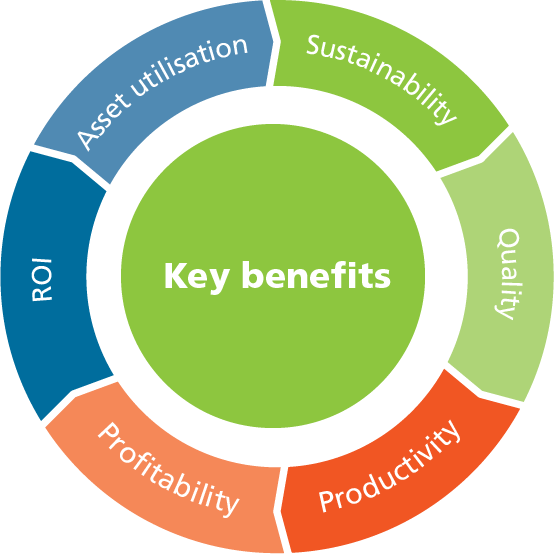
Asset Utilisation
- Increase overall equipment effectiveness
- Reduce unplanned downtime
Sustainability
- Lower carbon footprint
- Save energy
Quality
- Less waste
- Consistent final products
Productivity
- Increase production yield through efficient use of material
- Online instant monitoring eliminates manual testing
Profitability
- Reduce waste and energy
- Automate processes
Return On Investment
- Average ROI in 3 months
- No need for expensive ongoing maintenance contracts
Related Videos
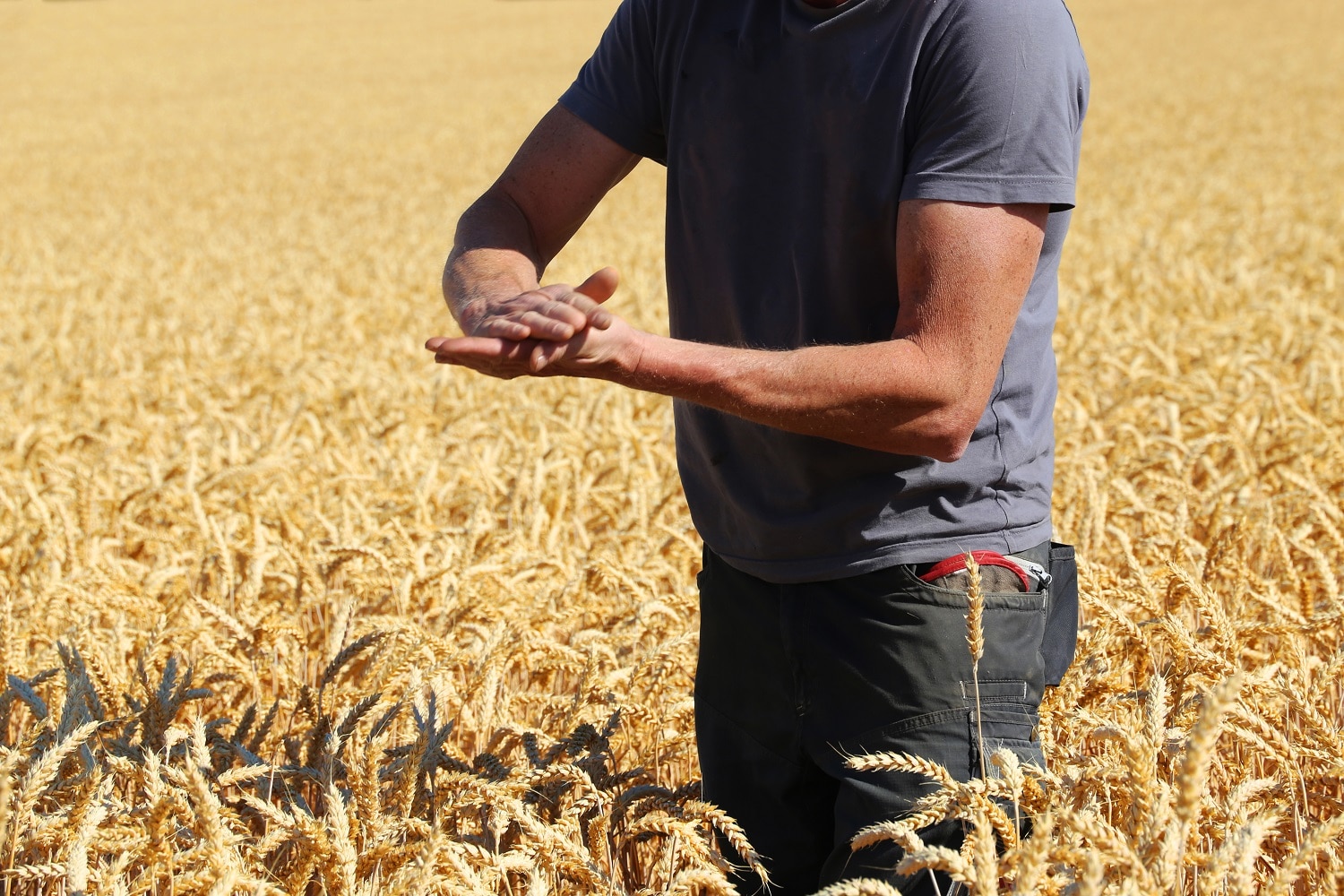
Why Should I Care about Moisture?
Edited 14 February 2024 Benefits of Measuring Moisture in Grain Processing Recent advances in moisture measurement technology are enabling forward-thinking businesses to achieve better control of their grain processing operations,…
Read more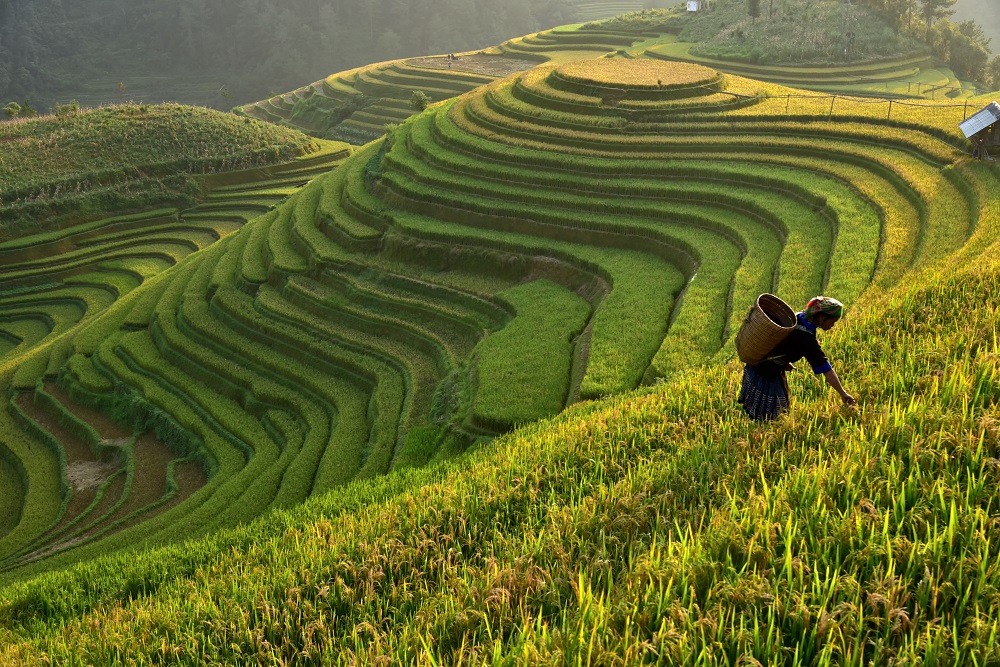
Moisture Measurement in Rice Production
Increasing Product Quality and Yield While Reducing Energy Costs India is the second-largest producer of rice in the World, second only to China, and processing approximately 155.682 million metric tons…
Read more