Controlling moisture in cereal grain drying processes
Cereal grains are used to produce animal feeds, flours, cooking oils, fuels, alcohol products, packaging materials and much more. World cereal production was forecast to be 840 Million tonnes (2023)1 with a projected value of $950 billion (2024) and an estimated growth rate of 6.2%2.
Managing the moisture content of cereal grains is crucial to maximising storage times, maintaining nutritional value and taste, reducing costs and waste and ensuring efficient use during further processing.
- Grain can be stored safely for longer
- Minimises the amount of energy required to dry the grain
- Maintains the nutritional value and taste
- Reduces harvesting losses such as cracked kernels
- Reduces dependency on weather conditions for harvesting
Where to measure moisture
Hydronix sensors are used to measure the moisture of the material entering and exiting the dryer. For a batch dryer system with a reasonably consistent incoming moisture, one sensor can be used on the output of the dryer. The sensor’s output can be used as the process variable of a feedback control loop for the dryer.
For systems with more fluctuation on the incoming materials this may be insufficient due to the time delay between materials entering and exiting the dryer. In this case another sensor can be installed on the input to the dryer to implement feed-forward control of the dryer with the value from the sensor on the output used for feedback error correction. This configuration allows the dryer control to respond more quickly to changes in incoming moisture and automatically adapt to unmodelled effects on dryer performance such as weather conditions.
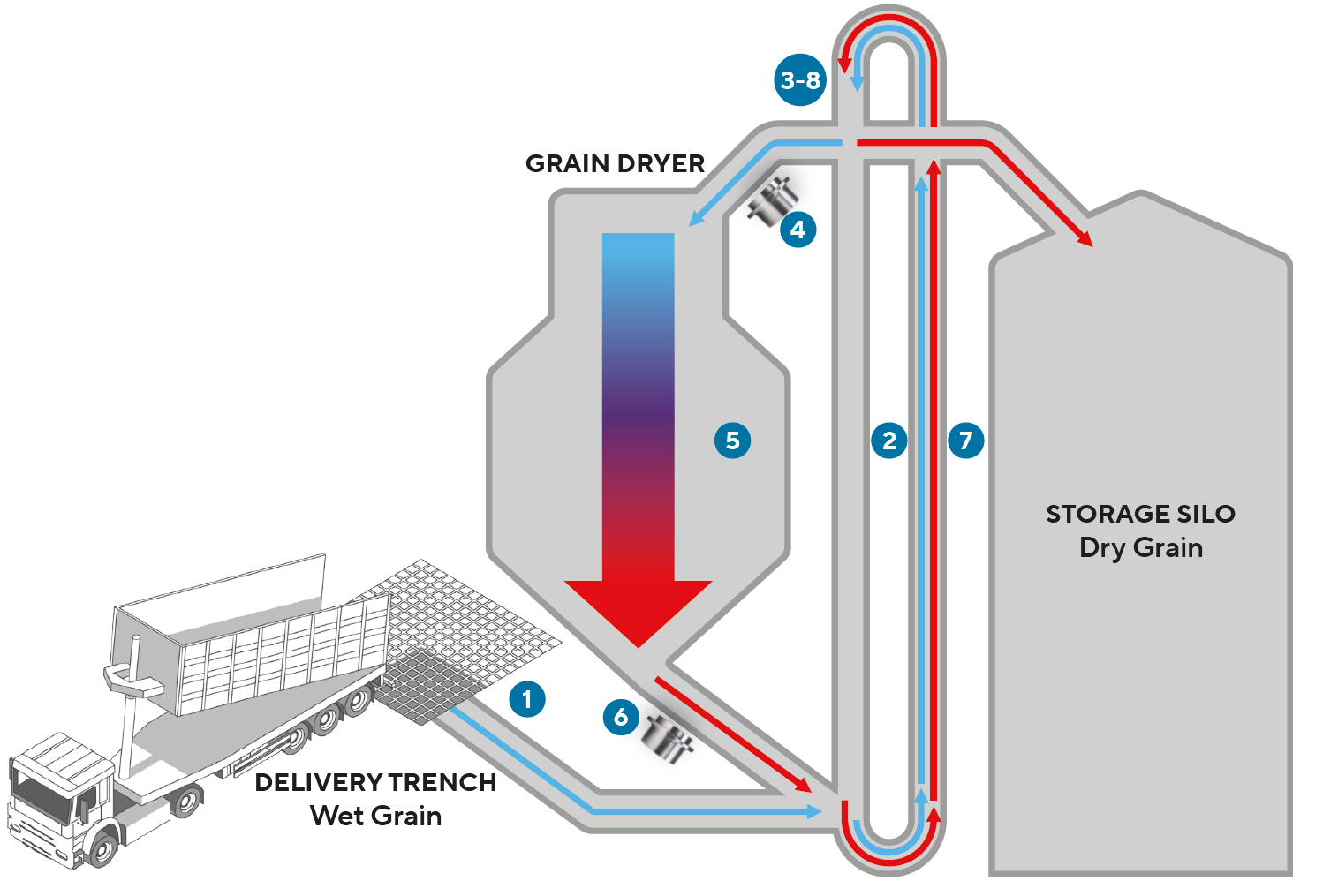
In Figure 1, Hydro-Mix XT sensors were installed in a re-circulating dryer (locations 4 and 6); using a Hydronix Ducting System to measure the moisture of the grain precisely throughout the batch, allowing the automation system to control the dryer accurately until the required moisture content was achieved.
- Wet grain is delivered with higher moisture.
- The material is elevated to feed the dryer.
- The diverter redirects the material into the dryer or to the silo.
- A moisture sensor is installed at the inlet of the dryer. In this location, the sensor enables the drying parameters (feed-forward) to be adjusted based on the material’s moisture.
- The material is dried.
- A moisture sensor is installed at the output of the dryer to enable precise PID feedback loop control.
- The material is elevated.
- Depending on the measured moisture level, the material is either diverted to the silo for storage or recirculated to the dryer for further drying.
Results after installing the sensor
A well-calibrated system will achieve accuracies better than ±0.5%. The results in Figures 2 and 3 were obtained from the output of a dryer processing barley, where an average accuracy of ±0.17% was achieved.
The moisture range was limited as the dryer controller was operating to maintain a target slightly lower than 12.5% to make the barley suitable for long-term storage.
US | Lab %M | Probe %M | Error |
---|---|---|---|
27.29 | 11.9 | 12.13 | 0.23 |
27.82 | 12 | 12.15 | 0.15 |
28.12 | 12.6 | 12.43 | 0.17 |
27.66 | 11.9 | 12.01 | 0.11 |
28.32 | 12.4 | 12.61 | 0.21 |
28.18 | 12.4 | 12.48 | 0.08 |
28 | 12.6 | 12.32 | 0.28 |
28.04 | 12.4 | 12.35 | 0.05 |
27.8 | 12.4 | 12.13 | 0.27 |
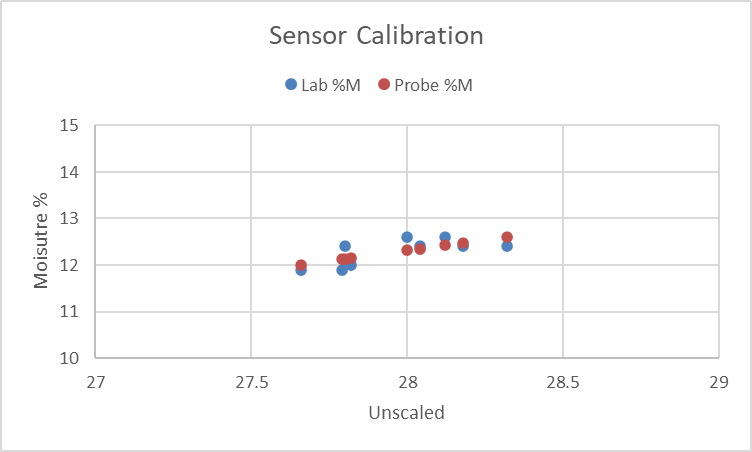
The Hydro-Mix XT and Hydro-Mix XT-EX
The Hydro-Mix XT sensor is constructed of 316 stainless steel with an abrasion-resistant ceramic measuring faceplate. Hydro-Mix XT sensors are designed to be flush-mounted in screw conveyors, chain conveyors, ducting systems and feed mixers.
The Hydro-Mix XT-EX has been specifically designed to measure moisture where an explosive dust atmosphere exists. It has IECEx certification and complies with ATEX and both NEC/CEC 500 and 505 standards in the USA and Canada.
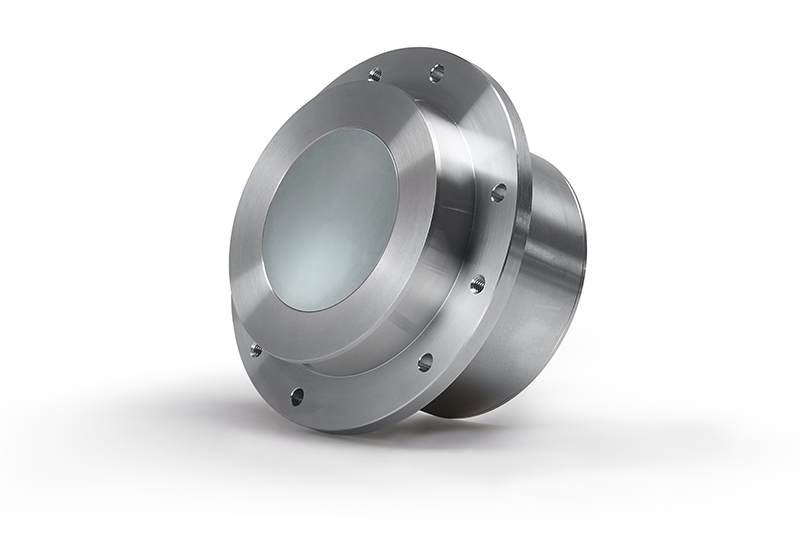
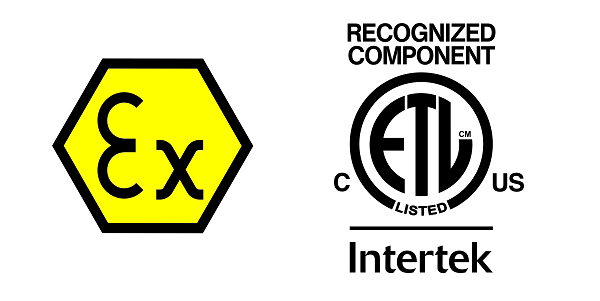
Hydronix sensors
All Hydronix sensors benefit from a unique digital measurement technology which provides a linear moisture measurement. The sensors incorporate advanced digital signal processing, enabling the sensor response to be adjusted remotely using Hydro-Com software. This ensures the sensor signal is clear, rapid and precise.
All sensors are designed and manufactured to have identical measurement characteristics. This makes them easy to integrate into third-party controls and to be used in numerous processes and materials throughout an organisation. They are not affected by dust or colour, and the microwave field penetrates the material for the most reliable and representative performance. The unique digital measurement technique also enables sensors to be further optimised for any given material by selecting from a range of measurement modes.
The sensors are designed to be robust and withstand harsh process environments. They will last for many years with little ongoing maintenance requirements. A typical installation has a financial return on investment of a few weeks and will reduce waste, reduce energy consumption and improve product quality.
Summary
Drying grain to a consistent target requires highly accurate sensors that can provide precise and repeatable measurements, resulting in a consistent product, a reduction in spoiled or wasted material, and better efficiency.
Hydronix sensors, such as the Hydro-Mix XT and Hydro-Mix XT-EX offer a purpose-built, robust and durable solution for grain drying and processing applications. These sensors can significantly increase profitability through waste reduction, yield maximisation and efficient use of energy.