Using Moisture Sensors to Control Slump
Concrete has a worldwide consumption of approximately 1 tonne per person per year, making it the second most consumed substance on Earth after water. It is comprised of three elements: aggregate and sand (filler), cement (binder), and water. When combined in the correct ratios, these elements create a chemical reaction that allows the concrete to set.
There are two distinct types of concrete: ready-mixed and precast. Ready-mixed concrete is typically manufactured in a batching plant and delivered to site by truck mixers for use in its freshly mixed state. Precast concrete is used to make individual cast concrete elements that typically form part of a larger structure. This type of concrete is made at a specialist plant and subject to more rigorous quality standards, and the control of moisture is a vital part of the manufacturing process. Both types of concrete require the manufacture to a specific recipe with the raw materials in the correct ratios to ensure consistency, quality, and strength.
The concrete producer will often use a slump test to check for workability, fluidity, and consistency of the concrete mix. Various factors will affect the slump test, including ratios of the aggregates and admixtures, and also moisture content. This article describes how the addition of digital microwave moisture measurement into the concrete plant can help produce consistent concrete batch after batch and, therefore, consistent slump properties.
Why is moisture control important?
Ideally, both the aggregates and the cement would be completely dry, so the amount of water required for each batch would be a set volume and the quality of the concrete produced would be identical batch after batch. However, aggregates are typically stored in a stockpile, usually outside. Although good storage can help, even for materials stored in covered bins, the moisture held in the aggregates will be in a constant state of change due to the inevitable effects of drainage.
In modern concrete batching plants, the amounts of materials required for the recipe are typically weighed, and the recipe is calculated using the assumed ‘dry’ weight of the materials. However, within the weighed aggregates, there will be an unknown amount of water. Although this article concentrates on slump, surplus water or moisture content in the sand and aggregates can also have dramatic effects on the water/cement ratio, the aggregate/cement ratio, the yield, and the colour of the mix. This will lead to inconsistencies in slump, strength, colour and quality, resulting in an inferior end product.
Why is the correct moisture calculation important?
If the concrete producer follows a set recipe using weighed amounts of aggregates and cement, then adds the specified amount of water to the mix, each batch produced will vary due to the unknown and differing amount of water held within the aggregates. For example, if a recipe specifies 1,000kg of aggregates unless these are 100% dry, the amount weighed will not be 1,000kg of aggregates but a mix of aggregates and water.
Moisture calculation
The only way to accurately determine the moisture of an aggregate by laboratory testing is to take a sample of the aggregate, weigh it (and its container) and dry the sample to evaporate the water, and then weigh the sample again. Normally, a second and third drying cycle is performed, as necessary, until there is no additional loss in weight (meaning that the sample is completely dry).
Calculations are then performed to correct for any additional moisture in the material s, ensuring that the aggregate ratio is correct according to the dry weight mix recipe. An example of the calculation is shown below using simple numbers to explain the concept:
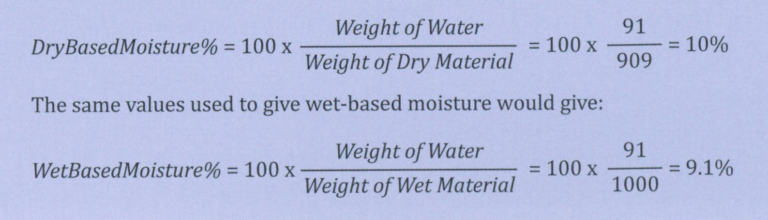
Weight of container= 500.0g
Total weight of wet sample and dish= 1,500.0g
Total weight of dry sample and dish= 1,409.1g
Loss in weight due to heating = 1,500.0 – 1,409.1 = 9 0.9g
Dry weight of sample= 1,409.1- 500.0 = 909.lg
Wet weight of sample = 1 ,500.0 – 500.0 = 1,000.0g
These values can be used to calculate the percentage of water in the material, see equation above. It can be seen how the measurement basis needs to be kept consistent through any moisture calculations. The benefit of working with dry-based moisture values is that it is much simpler to use these to calculate a target weight from the design weight.
How changes in moisture affect material ratios
The following examples demonstrate the effect of moisture variations in the aggregates on the ratio of materials in the mix. Other than total moisture, the ratio of materials in the mix is a key factor in determining the slump of the concrete.
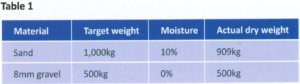
If a batch is weighed that has 10% moisture in the sand, and 0% moisture in the gravel (by the dry weight method), the proportion of sand to gravel is 1.8:1 (see table 1). However, if a second batch is dosed with sand at 0% moisture and gravel at 5% moisture, the proportion of the sand to gravel is now 2.1:1 (see table 2). This produces a significant difference in the ratio of materials between the batches and unless corrected, will directly impact on the quality of the concrete produced. It is essential, therefore, that the amount of water held within the aggregates is accurately measured and the dry weight of the material to be added to the mix adjusted accordingly.
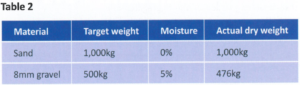
The final water added during the mixing stage may be adjusted based on the aggregate moisture content to achieve an accurate water/cement ratio and consistent slump. For optimum performance, however, separate control of moisture and water addition in the mixer is recommended.
Problems associated with variations in moisture
If the concrete mix is in the wrong proportions or the moisture level is incorrect, this will create issues with consistency, workability, or slump of the concrete. Ready-mixed concrete producers have to ensure that their concrete will still be at the correct consistency and able to produce the correct slump and strength when delivered to the customer.
For precast concrete producers, variations in moisture will also cause problems with moulds and formwork when manufacturing components. Examples of this include pipes collapsing after the core are removed or block falling apart after exiting the block machine.
Hollowcore concrete slabs are also noticeable examples where the concrete can sag or deform as the hollowcore machine moves down the line.
Another problem associated with moisture variation in aggregates is that the surface area of the aggregates will change (i.e. fewer aggregates than expected). This is of great importance when adding colour to a batch of concrete, as coating of the surface area by the pigment will vary as the mix proportions change, causing colour inconsistency across different batches that can be costly to put right.
What should moisture measurement method be used?
Although the results from laboratory drying tests are accurate, they are time-consuming. Moreover, this method does not allow for any changes to be made to material ratios in real-time. Several different methods of moisture measurement can be used to automate the process (e.g. capacitive, resistive, infrared, microwave, etc.), all of which have their own advantages and disadvantages. One of the most popular systems is microwave, which is not affected by impurities, colour, particle size, or temperature, and, arguably, has proved to be the most accurate.
Cost benefits using microwave moisture measurement
As well as an immediate improvement in the quality and consistency of the concrete batch after batch, the concrete producer will also benefit from increased profitability. This can be defined either by a reduction in the amount of spoilt material or waste or by an improvement in the efficiency of the material being used. Benefits include:
- Reduction in the number of spoilt materials from inconsistent mix ratios
- Reduction in the amount of cement used to reach correct strength
- Consistent, repeatable quality
- Consistent workability and slump
- Consistent surface finish
- More efficient use of colour additives.
Conclusion
The addition of digital microwave moisture measurement and control into the process provides a simple and cost-effective solution for the concrete producer. The resulting concrete will be consistent batch after batch, improving product quality and reducing wastage or spoilt materials. Moisture control can easily be installed in new or existing plants, with the return on investment often being seen just months after installation, depending on the output of the plant.