Moisture Control in Woodchips
The moisture in wood stockpiles varies constantly with local environmental conditions, both during harvesting and storage. Working with the correct moisture of wood is important to prevent damage to process equipment, so measuring the moisture online with precision sensors ensures optimum efficiency.
Typical applications include biofuel for boilers for CHP or power generation applications, syngas production, and processing wood into intermediate products, such as charcoal briquettes and wood pellets.
Benefits of Moisture Control:
- Consistent quality of the woodchips
- Ensure correct moisture for storage, reducing the risk of spoilage
- Increased control of the final product
- Lower wastage and product degradation
- Direct, continuous, real-time control of the burning process
- Optimised combustion
Where to Measure Moisture?
After the woodchips are delivered, they are dried before entering a Combustion Chamber where they are burnt to generate heat which has multiple uses (e.g. hot water or steam for power generation).
The excess heat from the process is also fed back into the dryer to reduce the energy input.
Common measurement locations are:
- Dryer Input: measuring moisture as the material enters the dryer enables control of the operating temperatures, maximising its efficiency. Rejecting wet material also avoids batch failures caused by excess steam production.
- Dryer Output: measuring the material leaving the dryer allows a feedback control loop to be set up, resulting in a stable output moisture and optimising the process in the Combustion Chamber.
The dryer process control loop uses the error between output and a pre-set target value to adjust for unknown variables.
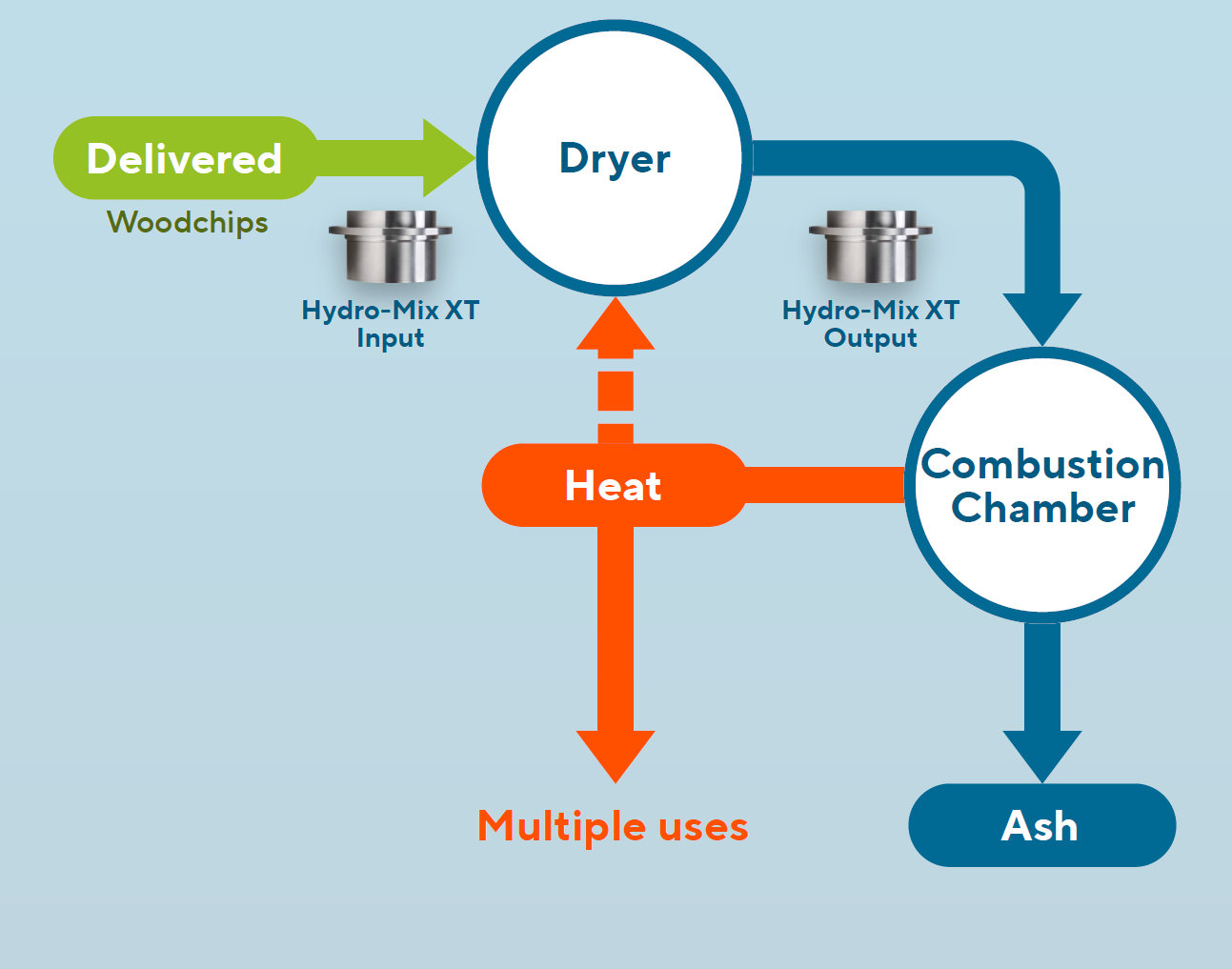
Recommended Installation
Figure 2 and Figure 3 show the recommended installation point for a sensor measuring moisture in woodchips in the screw conveyor.
The sensor is installed at 30° from the underside of the screw, just before the sampling point. It is essential that the sensor is located so that the ceramic disc is continuously covered by at least 100mm of material.
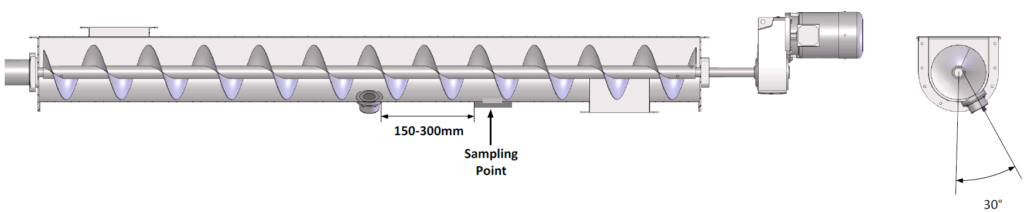
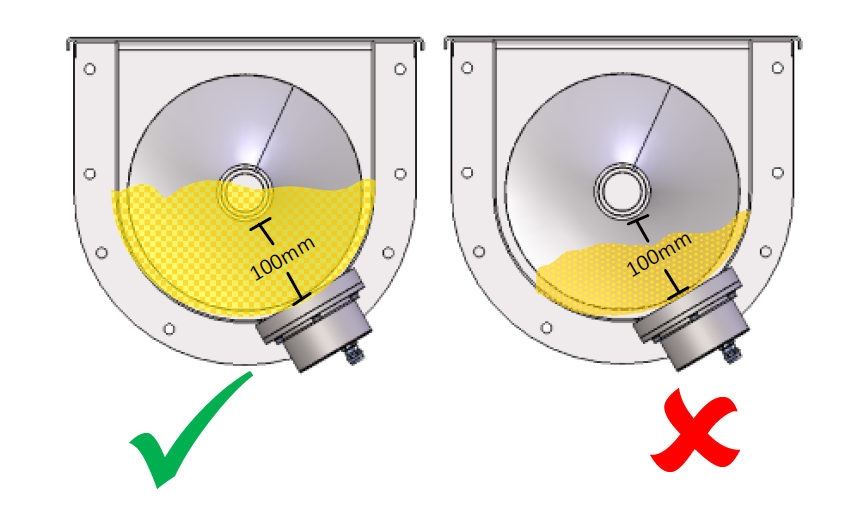
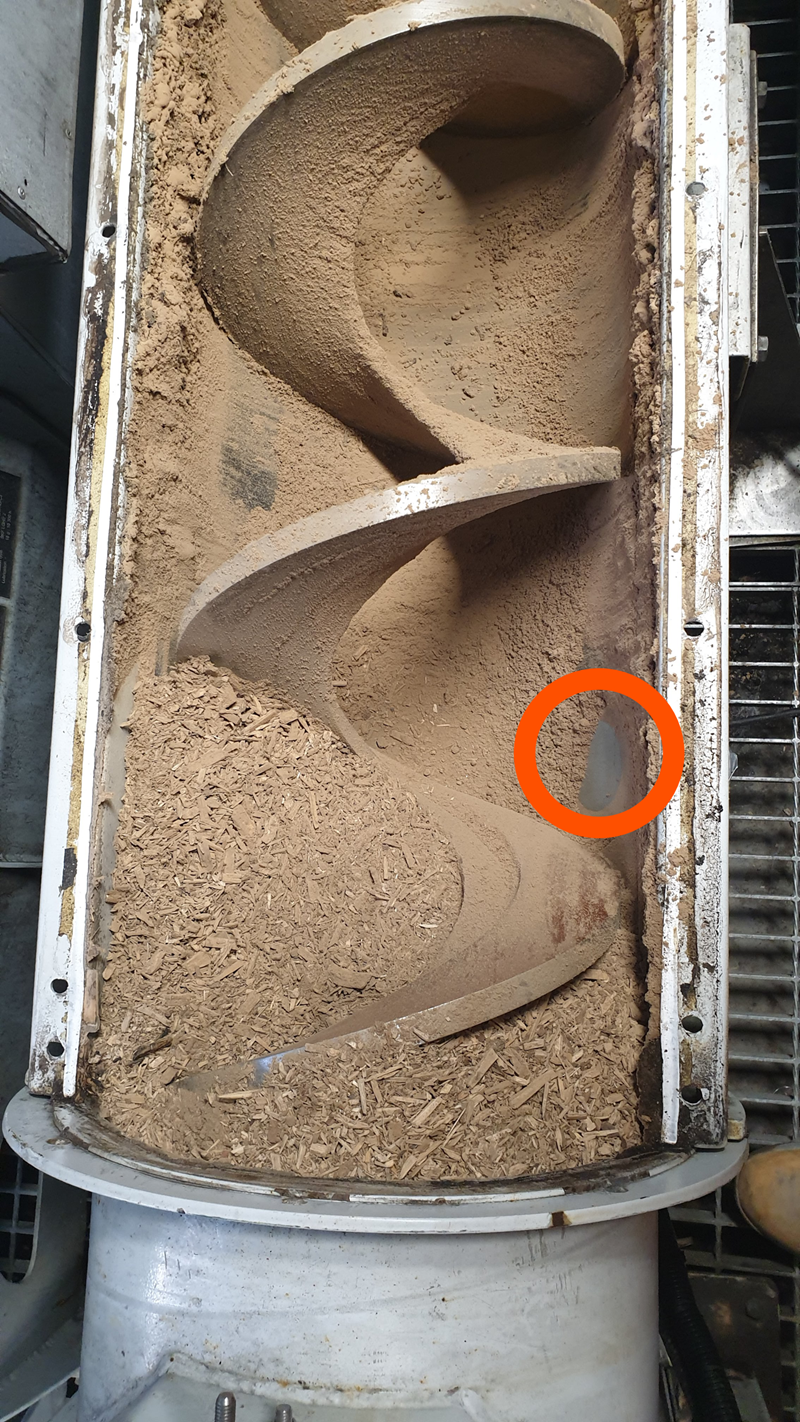
Industry Expert Opinion on Moisture Control
“…the moisture content is considered the most pressing one as it directly impacts the energy content, storage stability, and handling properties of the raw and finished products.
Therefore, accurate wood chip moisture content prediction can help optimize the drying process and reduce energy consumption.”
Abdur Rahman, Mohammad Marufuzzaman, Jason Street, James Wooten, Veera Gnaneswar Gude, Randy Buchanan, Haifeng Wang1
Conclusion
Installing moisture measurement sensors in woodchip plants can maximise efficiency and prevent wastage/degradation.
The Hydro-Mix XT and the Hydro-Mix XT-EX for explosive atmospheres are purpose-built, robust, and ideal solutions for woodchip applications. These sensors can significantly increase profitability through waste reduction, yield maximation and efficient use of energy.
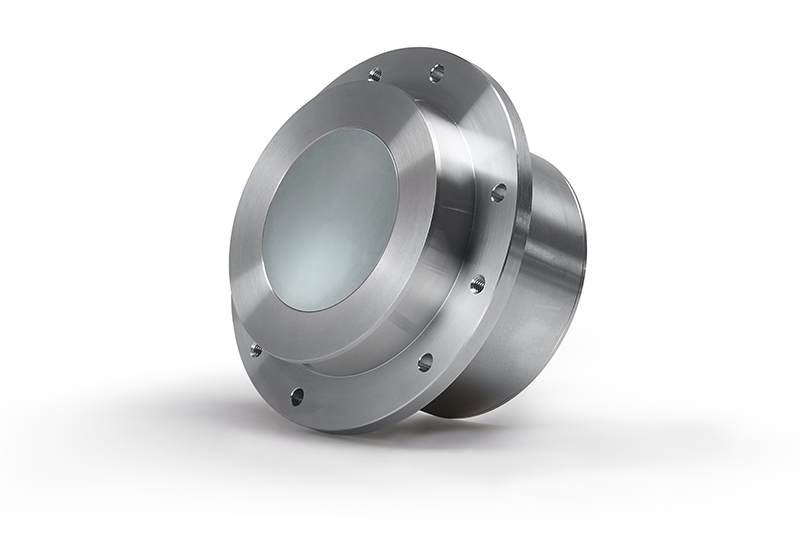
- Abdur Rahman, Mohammad Marufuzzaman, Jason Street, James Wooten, Veera Gnaneswar Gude, Randy Buchanan, Haifeng Wang (January 2024). A comprehensive review on wood chip moisture content assessment and prediction
https://www.sciencedirect.com/science/article/abs/pii/S1364032123007001 ↩︎