Moisture Control in Clay Brick Production
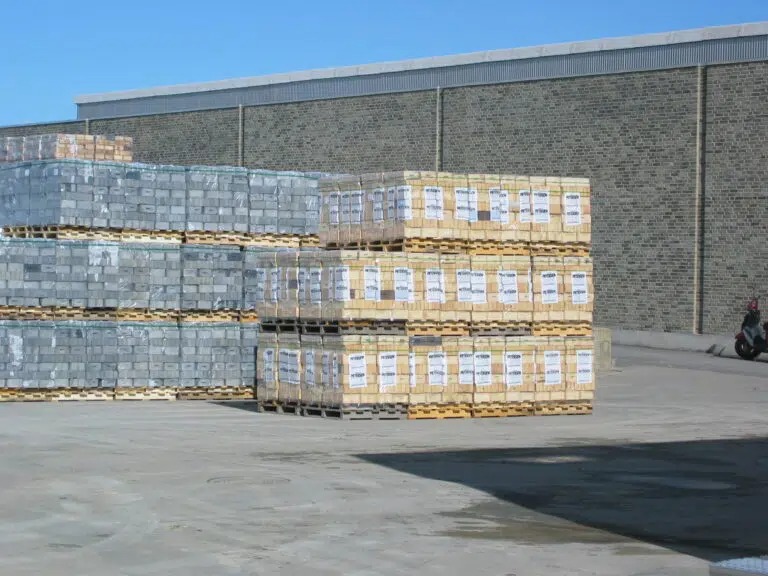
Bricks have been in use for thousands of years and form the basic structures of our civilisation. Originally, the brick making process was manual and involved clay being moulded and then dried in the sun. Today, although this process still exists in some parts of the world, it is now mainly automated, using large machines to mix, cut and mould the clay to shape before firing in kilns.
All raw materials have a different capacity for holding moisture. This can depend on the geographical location of the source material, how it is stored, the humidity in the atmosphere and also the different particle size. Moisture levels can also vary between batches from the same source. Because raw materials are so variable in their moisture content, each batch of bricks will require a different amount of water to be added to the mix to ensure the right consistency at the end of the mixing process.
Why moisture measurement is important
The moisture content of the mix is crucial if a quality end product is required and to produce consistent results with every batch. The correct water to aggregate ratio will allow good, dense compaction of the clay, and the brick will release easily from the mould. Too little water and the brick will crumble, too much water and the brick will sag or fall apart.
For centuries, the brick industry has been striving to find a method of maintaining a consistent moisture content in the extrusion or forming stage of manufacture. Traditionally, the consistency of the clay has been controlled manually using the power consumption of the mixer. Problems such as the effects of temperature and mixer-blade wear make this controlling method unsuitable and mean the manufacturer is unable to guarantee a consistent mix batch after batch.
Ideally, a moisture control system should be able to accurately detect moisture in raw materials, preferably at different stages of the manufacturing process, be easy to maintain and tough enough to withstand the harsh, abrasive nature of the raw materials and the mixer environment. Customers requiring accuracy in their mix have successfully used Hydronix Hydro-Mix microwave sensors, to automatically control the moisture addition throughout their process and improve both consistency and throughput of production. This application note describes how Hydronix sensors have successfully been used during processing at a brick factory in Europe.
Benefits of moisture measurement
- Consistency: correct mix consistency is easily repeatable, batch after batch to the required quality standard.
- Cost Reduction: if moisture content is known during processing this will assist manufacturers to calculate the required drying time before firing. This reduces the number of rejects and therefore increases production levels.
- Environmental: if moisture levels are known, then the amount of fuel required to remove any excess moisture during fi ring can be accurately calculated and adjusted if required. This can lead to reduced levels of energy used and further cost savings.
The brick manufacturing process from raw material to finished product
A typical brick making process can be simplified down into several stages:
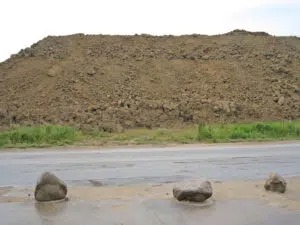
- The raw material is transferred from the stock pile into a storage bin. The bin is opened and the raw material is transferred by conveyor belt to the next stage of the process. This may be to a grinder where the aggregates are ground to the correct particle size or direct to a twin shaft mixer.
- Water is added at the first mixer stage, and steam is injected to heat the material to reduce it’s viscosity. With the addition of water, the raw materials at this stage can now be called clay.
- The clay is transferred to a ribbon mixer where additional water is added to achieve the correct consistency. This fi nal mix (with approximately 20% moisture depending on individual manufacturer’s requirements) is extruded from the mixer outlet and cut into small lumps ready for pressing.
- The lumps of wet clay are fed through the press and shaped into bricks. Excess material, called slurry is scraped off and returned back into the mixer to be re-processed. The green bricks are stored for drying before fi ring in a kiln and fi nally completing the manufacturing process.
Typical locations for installing moisture sensors
Three Hydro-Mix sensors were installed at this plant in Europe to provide accurate moisture control throughout the entire mixing process. Installation of the sensors is simple: a small hole is cut into the side or floor of the mixer and a fixing plate welded. The Hydro-Mix is then fitted into place with adjustments to height made if required. An RS485 cable sends the sensor readings back to the control system. Designed for permanent installation, the Hydro-Mix sensor can be removed if required for maintenance.
The simple process diagram below shows where the sensors have been installed at this plant, although the exact location and positioning of the sensors will vary from site to site depending on plant equipment.
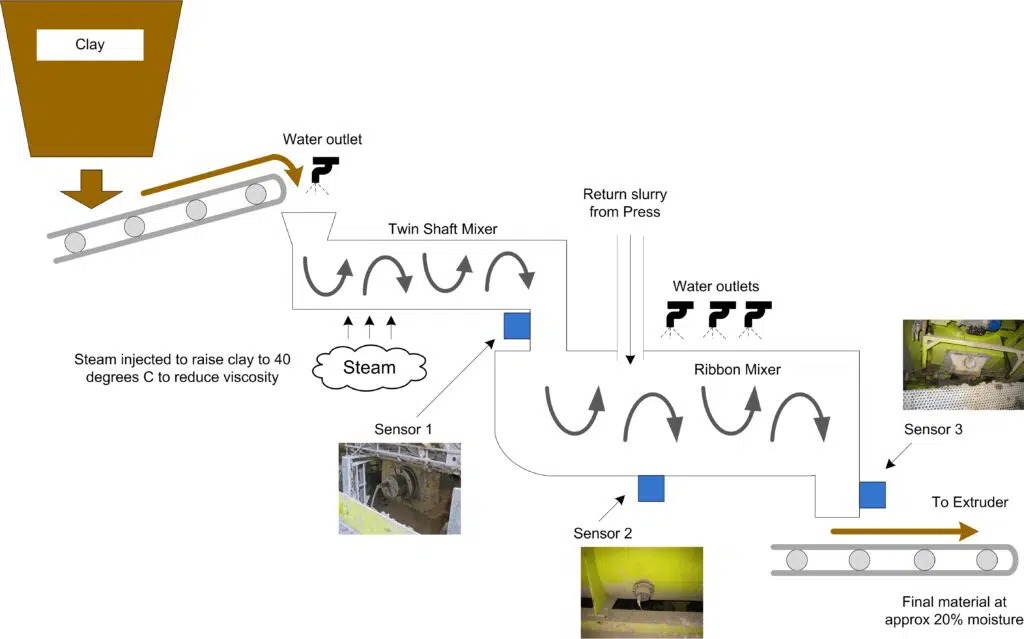
Sensor 1: – At the output of the twin shaft mixer
Water is added to the raw material as it enters the mixer at the start of the mixing process. Readings from the Hydro-Mix sensor are used by the control system to maintain consistent moisture levels in the raw materials.
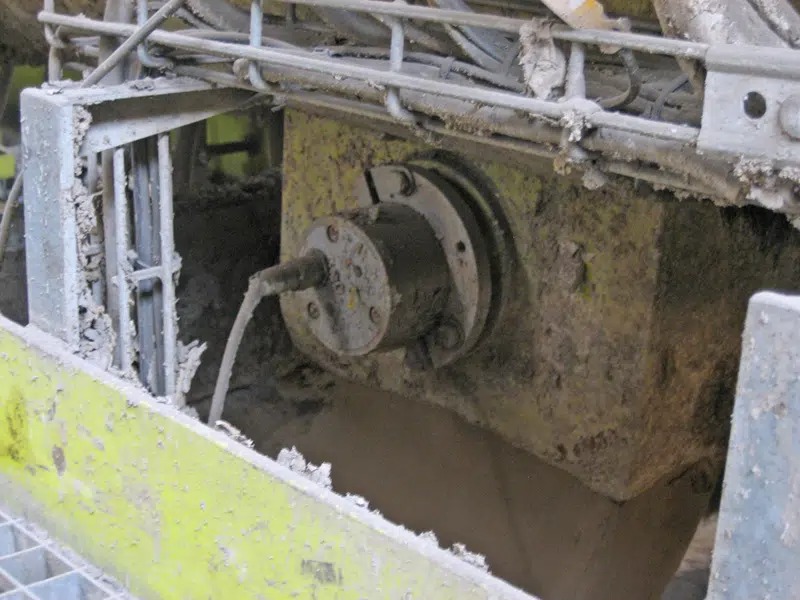
Sensor 2 – Halfway along the ribbon mixer
Sludge from the press is pumped back into the mixer, which changes the moisture content of the clay and its consistency. The readings from the Hydro-Mix sensor are used to ensure that the correct amount of water is added to the ribbon mixer.
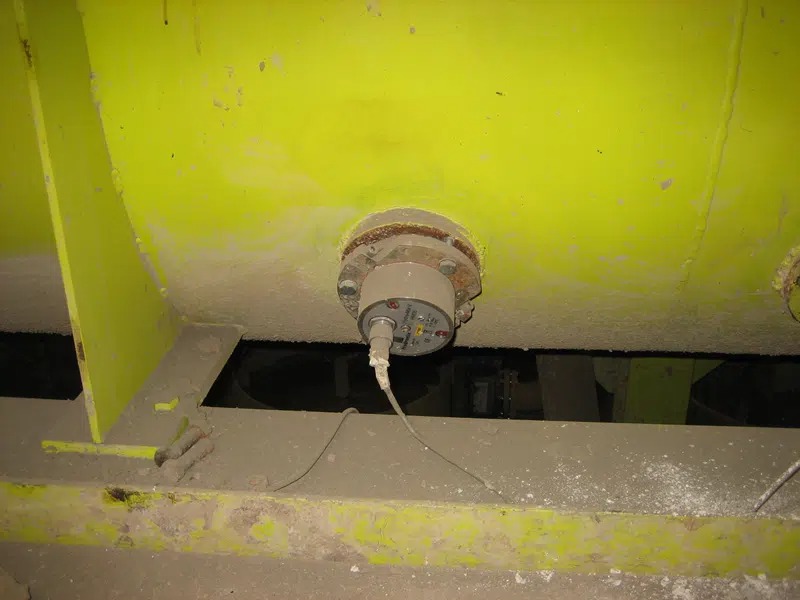
Sensor 3 – At the output of the ribbon mixer
A further Hydro-Mix sensor is installed at the outlet of the ribbon mixer to make the final check on moisture before the clay is passed through the extruder. The readings from this sensor should confirm that the mix consistency is correct.
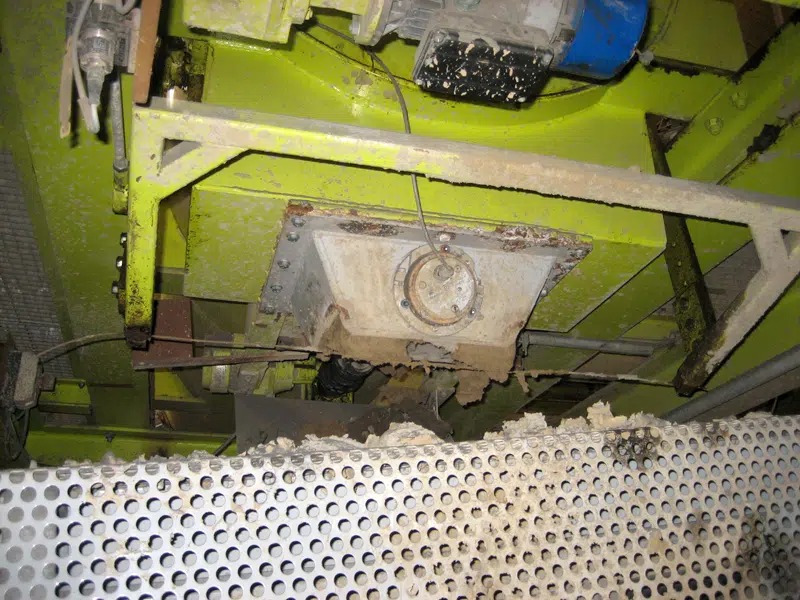
Hydro-Mix sensors
Hydro-Mix sensors were originally designed for use in mixers in the concrete industry but perform equally well in other types of mixers as well as chutes or screw conveyors. They are built of rugged, hard wearing steel with a ceramic faceplate and easily withstand the turbulent environment of a mixer, so are ideally suited to brick manufacture. The Hydro-Mix sensor is flush-mounted with the surface and has a flat faceplate so that the material can flow freely over it as it passes along the manufacturing process without causing any build-up.
Conclusion
Many brick manufacturers are now participating in quality management programmes as well as looking at ways to increase production levels while reducing costs. The installation of a Hydronix microwave moisture control system can help them to achieve consistent, quality products while reducing costs in the reduction of wasted materials and potentially lower fuel costs.