Controlling moisture in corn/maize
Corn, also known as maize, is one of the world most cultivated crops. Corn can be used for human consumption, animal feed and fuel. It can be heavily processed to produce products such as flour and biodiesel or sold as whole grains.
The need to measure the moisture content of corn
Corn processing benefits from moisture control for several reasons:
- Correct moisture levels for storage, increasing shelf life and inhibiting mould growth
- Increasing the reliability of the milling process
- Increased product control
- Reduction in waste and spoilt product
- Direct continuous, real-time, control of the drying process
- Monitor the material during the entire process, from delivery to the final product
Control of the moisture during processing and for storage is vital to produce a final product suitable for its intended market.
The benefits of installing microwave moisture measurement sensors
- Dryers can be used more efficiently thereby reducing energy costs
- Improved and consistent product
- Reduction of spoilt/wasted material
- Not affected by dust or colour
- Real-time automation of the drying process, reducing the need for manual intervention
- Reduced process downtime
Recommended installation
Hydronix sensors can be installed at various stages during processing of corn:
- Raw material delivery to site
- Before and after storage
- Before and after drying
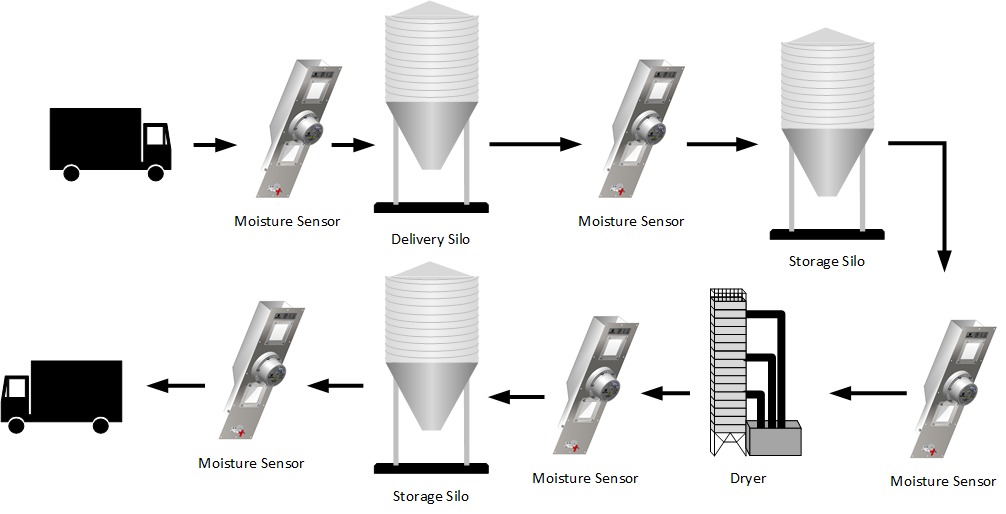
In the following example, a sensor is installed at a storage site. The material is moved between silos to be discharged or to undergo further processing.
A Hydronix Hydro-Mix XT sensor is installed in the discharge chute that feeds a conveyor belt transport system. A Hydronix Ducting System has been utilised to control the material flow and to ensure the sensor is exposed to enough material to calculate the moisture of the corn. The sensor is connected directly to the PLC to enable the control system to direct the material to a suitable silo or to discharge it to a waiting lorry.
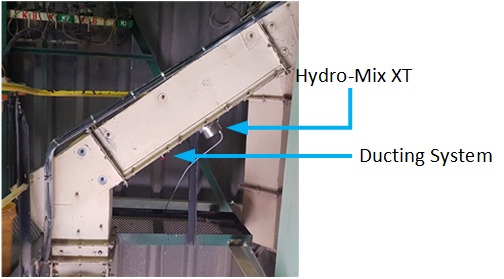
Result after installing the sensors
A well-implemented installation will measure the moisture levels of the materials to an accuracy of +/- 0.5%, enabling the production process to be controlled more precisely.
Real-time control of the silo storage moisture levels (as opposed to waiting for oven tests) ensures there is instantaneous control of the corn and adjustments can be made rapidly. When drying the corn, there is a reduction in the amount of substandard or wasted product caused by the time delay between periodic sampling and subsequent dryer adjustment.
Hydro-Mix XT sensors
Hydro-Mix XT sensors are constructed of stainless steel and have an abrasion-proof ceramic measuring faceplate. The sensor is designed to be installed flush-mounted with the surface of the mechanical material transport system allowing the material to flow freely over the measuring faceplate without causing any build-up.
Hydronix sensors have configurable parameters for built-in filters to reduce and eliminate noise caused by flow disruption. The sensor features numerous output options available directly from the sensor or via Hydronix gateway devices. The Hydronix Hydro-Com software enables simple set-up and configuration of the sensor using a PC or laptop and USB connection.
Conclusion
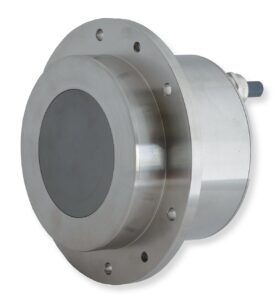
The inclusion of a microwave moisture measurement system into the existing process will help you to:
- achieve consistent quality products
- reduce the number of spoilt materials
- provide instant savings
- repay its capital expenditure in a very short time.