Are All Moisture Sensors Equal?
When working with materials that can hold water, it is always important to know how much water is contained inside it. Depending on the size of the particles, storage method, temperature and many other factors, some materials can hold more water than others.
The moisture content influences many processes, so let us focus on of a common example: the measuring of materials by weight. As the moisture naturally varies during material storage, knowing it allows us to determine exactly how much dry material is in the measured amount.
The solution is simple, as using an online sensor makes it possible to know the moisture in the material. Measuring the water content is an indirect measurement, meaning that it is calculated from another measured property, so to do this accurately other factors need to be kept as constant as possible:
- Material composition
- Particles size
- Pressure on the sensor
- Flow speed
- Position of the sensor
For this reason, it is key to calibrate the moisture sensors for each material after the final system installation. The calibration must be realised by accurate lab tests, as calibrating any sensor with another different sensor can cause a sum of errors resulting in incorrect calibrations, defeating the initial objective completely.
Independently from the measurement method used in the process, it is critical to completely remove moisture from the sample to reach the dry weight during the lab test, as this is what will be used while calibrating the sensor to define the moisture reported by the sensor.
But are all the sensors equal?
There are many moisture sensors available on the market, and these different technologies can be summarised in five categories:
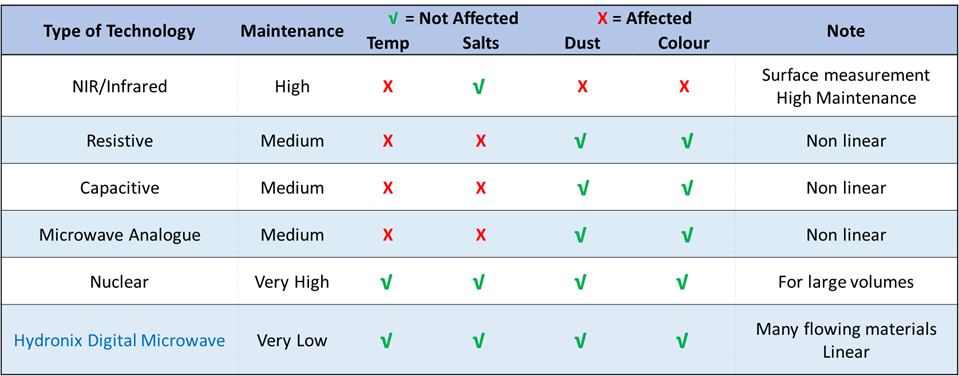
- NIR/Infrared – When comparing different types of sensors that are available on the market, NIR sensors are higher in installation and ongoing maintenance costs. This technology only gives a surface reading, which can be affected by changes in the material colour, ambient light and temperature. This can be offset by the ability to read other online measurements from the sensor, such as protein and fat content (amongst others).
- Resistive and Capacitive – These sensors both use electromagnetic waves at low frequencies to determine the electrical properties of the materials, but these characteristics do not have a linear relationship with the water content, decreasing the useful working range. This technology is also affected by salts, density, and temperature changes, which makes these kinds of sensors very sensitive to variations in the material.
- Microwave Analogue – Many Microwave sensors use older analogue measurement techniques using a fixed-frequency microwave that reacts with the water in the material. Since this method is also based on determining electrical characteristics, it is non-linear and affected by temperature and salt changes.
- Nuclear – This technology is very expensive, and whilst it gives a very accurate measurement, it is only for large volumes of space and is not suitable for smaller ducts or conveyors. They also need regular maintenance by specifically qualified and certified personnel.
- Hydronix – Microwave Digital Measurement sensors use a specific multifrequency measurement technique, which is linear with the moisture change in the material. This technology is not affected by salts, dust, or colour and is also very stable over time and as temperature changes, which makes it very simple to install, calibrate, and use. This type of sensor will need a good, consistent flow of material to measure, and this can be easily achievable by mechanical design.
An essential, often overlooked, difference in the digital microwave technology is the linearity and stability of the output. Resistive, capacitive, and analogue microwave sensors have a nonlinear output making them very difficult to calibrate as they require numerous points to design the curve. Nonlinearity also implies low accuracy at the wet and dry end of the scale (Figure 1).
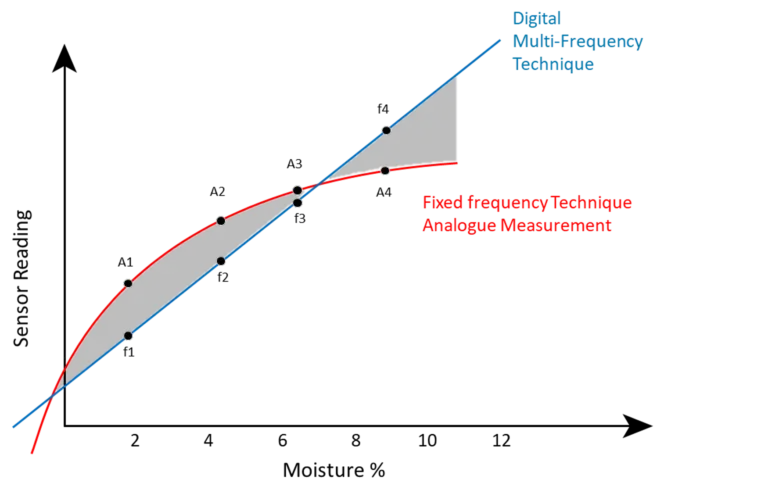
Sensors with a digital measurement technique have a linear output, meaning that the sensor reading and water content are directly and proportionally related. This method allows systems to achieve optimal calibration with a few points. In theory with a linear system, it is possible to achieve calibration with only two points.
After these considerations, it is possible to define the ideal requirements of the moisture sensor:
- In-line with multiple readings per second, providing quick feedback for the control to adjust every batch.
- Robust, made with high-quality materials to withstand tough industry conditions.
- Linear output, stable over time, accurate in every condition and simple to calibrate.
- Store multiple calibrations to be used with different materials.
- Ability to measure into the flow of the material.
- Unaffected by dust, colour, or variations in salt and mineral content.
- Self-contained and easy to integrate into existing systems.
- Low maintenance and cost-effective.
- Able to monitor and configure remotely for flexible connectivity and analysis.
Thanks to the expert research and development team at Hydronix, all the above characteristics can be found in Hydronix microwave sensors which incorporate a unique digital microwave technology made to last in the harshest conditions.