Capturing and using moisture measurement data: ‘Big Moisture’
For many industries, measurement and control of the moisture in materials is vital. Whether it be adding the incorrect amount of water spoils the product or over-drying it wastes energy, moisture measurement matters. Within a larger process, moisture monitoring and correction often needs to happen at different stages because the moisture content before and after each sub-process can be critical to the quality of the final product.
Achieving the balance right requires instantaneous, online access to moisture data throughout the process. Moisture content of materials entering and exiting processes can change rapidly, requiring an instant response to maintain the quality of the final product and the efficiency of the process.
Online moisture measurement offers scope for immense benefits, including:
- Optimisation of recipes to efficiently use raw materials
- Cutting the amount of spoiled material
- Lowering energy costs
- Reducing processing time
- Increasing production rates
- Higher quality and greater consistency in end products
- Maximising profitability
The need for connectivity
Today, digital moisture sensors that offer highly accurate, real-time data are commonly deployed throughout processes. This avoids the need for manual laboratory testing and enables automated control of moisture. Customers are increasingly demanding real-time connected solutions and wish to use networking technologies to connect all their sensors to the plant’s monitoring and control system.
Consolidating the data from all the moisture sensors throughout the plant and making this information available online and accessible from anywhere, ensures not only that individual processes can be monitored and maintained but that interacting processes may be monitored and the entire plant optimised in real-time. Historic data can also be easily collated and compared to other plants to review and improve efficiencies across the breadth of the company.
Monitoring Sensor Performance
If the data from sensors is to be trusted, it is important to be able to monitor and assess the sensors’ performance. Smart sensors must include remote access and built-in diagnostics data to ensure that issues affecting measurement such as blockages or damage to the sensor can be quickly identified and rectified.
Bridging the gap between plant and office
The centralisation of critical moisture data ensures that process engineers always have a current view of precise process conditions and allows the control system to respond rapidly and automatically to correct any issues or improve performance.
Using online data, stored either locally or in the cloud, it is possible to record, monitor and analyse the data over time, allowing trends to be identified and further improvements to plant performance to be achieved. If the organisation has several plants, performance can be further improved by comparing the data for each of them.
Requirements for connecting sensors
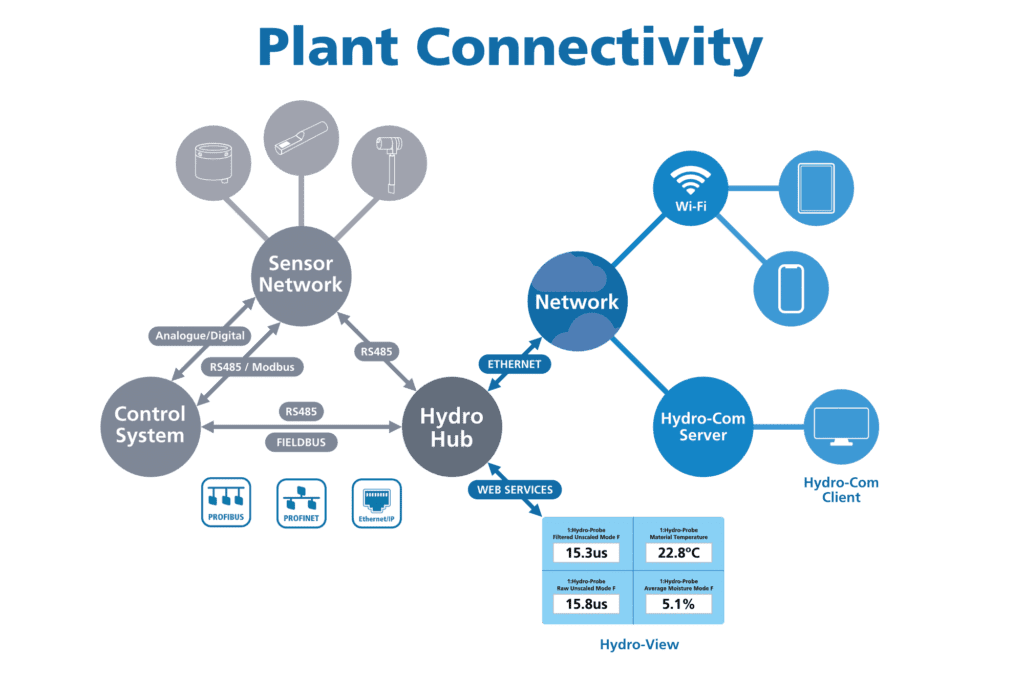
Hydronix Sensors have numerous ways of connecting to the plant control systems. The most basic systems use the sensors’ analogue loop output. More advanced systems use the selectable Modbus option, a protocol running on RS485, designed to deliver optimum performance in a manufacturing environment. The sensors can also connect using various other industrial communication protocols.
Most people are used to hearing of the Internet of Things (IoT) and Ethernet TCP/IP for connecting devices to the web and between homes and offices, the Industrial Internet of Things (IIoT) enables the same types of connection in a far more robust, secure, and controllable manner.
Because of the different standards used for data communication between industrial and home or office environments, connecting industrial sensors online requires a bridge between the two different types of networks to facilitate the connection and ensure the security of both systems.
Easy connectivity

The Hydronix Hydro-Hub™ is a solution that provides a bridge to easily transfer moisture data between industrial and office-based IT networks. Designed to add flexibility and to future-proof existing and new investments, it ensures that all industries that rely on accessing moisture data can benefit from the advantages of connected Hydronix sensors.
The Hydro-Hub acts as the central point to connect up to 16 sensors simultaneously to online systems with an Ethernet connection. Multiple Hydro-Hubs may be deployed across a local, or wide area network, to connect devices within a single plant and from various plants around the world. It offers an easy method of moisture data collection, sensor configuration, diagnostics, and calibration selection.
To simplify the access to the sensor data, a built-in web server allows direct access from a tablet or PC, while a web API interface provides for remote connections to data storage and online plant management or monitoring systems.
The Hydro-View is a similar product that additionally incorporates a 10.1” touchscreen to view and interact with the sensors. The Hydro-View allows sensor integration with a control system and also connection to IT systems as well as being a standalone unit for recording sensor data.
Conclusion
As with other process control parameters, effective moisture control relies upon accessing reliable, high quality, real-time data. Network-enabled devices give the industry the tools to monitor and adjust plant-wide variables with very significant benefits including, savings in energy carbon footprint, maintenance, and material costs.
To help industries achieve these benefits, leading sensor manufacturers, such as Hydronix, provide highly accurate sensors with networking technology, high-quality training materials as well as global support and service.